你知道吗
你在路上见到的冷藏箱
超过一半是中集造
你吃的进口牛肉喝的进口牛奶
都是靠这台“大冰箱”保鲜运输
造1台冷藏箱需要多长时间
答案是,220秒
为何这么牛
今天为大家揭开谜底
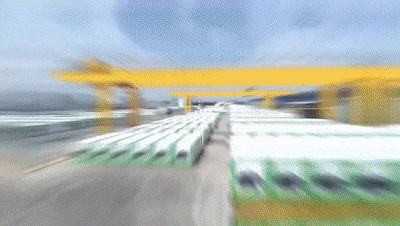
12月6日,工业和信息化部、国家发展改革委、财政部、国务院国资委、市场监管总局联合公告,发布了《2023 年度智能制造示范工厂揭榜单位》名单,中集集团旗下青岛中集冷藏箱制造有限公司(以下简称:青岛冷箱)成功入选国家级“智能制造示范工厂”,这也是中集集团首家工厂获得此“国字号荣誉”。
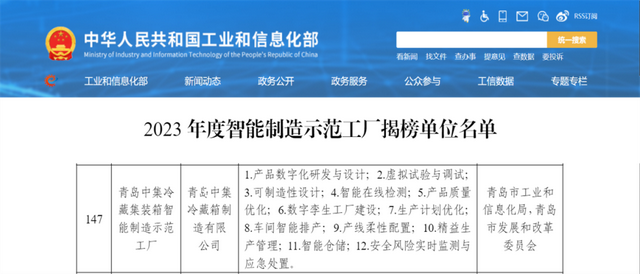
此次评选是上述五部门为贯彻落实《“十四五”智能制造发展规划》联合发起的,以揭榜挂帅方式建设一批智能制造示范工厂和智慧供应链,在各行业、各领域选出和树立一批排头兵企业,推进智能制造高质量发展。
数字化替代“老法师”的小木棒
目前全球贸易90%的运输量,都是通过海运完成。中集集团作为全球最大的冷藏箱制造商,市场份额保持行业领先,其中,青岛冷箱在中集的两家冷藏箱生产基地中体量最大。
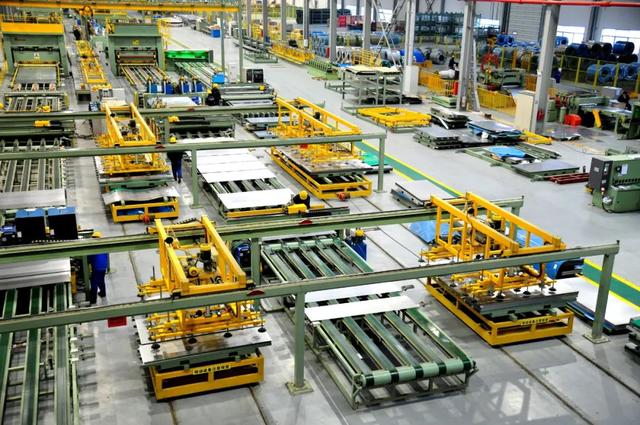
冷藏箱,可以看作是一个移动的特大号“冰箱”,运输过程中要经受风吹日晒,对冷藏、保温性能要求非常高,除了需要专用温控设备进行温度调节外,还需特殊材料进行隔热保温。聚氨酯泡沫是目前全球应用最广泛的冷藏箱保温材料,它像一层“羽绒服”,能够隔绝车厢内外的热量交换,让车厢内部始终保持低温。
保温层的发泡工艺是冷藏箱中最核心的技术。钢质冷藏箱由内外两层钢板,加上中间聚氨酯发泡料组成三明治结构,整个发泡过程是闭式浇筑。
发泡是一个化学反应,混合液需流动覆盖到接近40尺的钢板,化学反应不充分,会出现钢板和泡沫粘结不好,导致分层、漏泡等现象,影响冷藏箱的保温效果。但钢板和保温层均是不透明材料,如何查看发泡过程中化学反应是否充分?
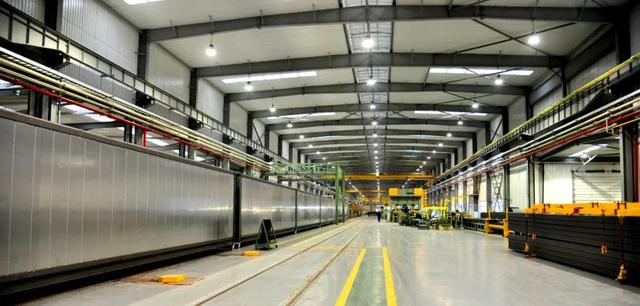
过去,依靠发泡工程师庄兴民这群“老法师”,拿着小木棒敲打冷藏箱,“闻声辨病”。而称得上“老法师”的人至少需要10年以上发泡工艺经验,能够符合条件的人在整个行业屈指可数。
然而,影响发泡工艺的重要参数40余种,甚至有的参数人工难以观测,过于依赖人工经验,可能会出现判断错误,导致有问题查不出来的现象偶有发生。
这个痛点如何解决?中集集团开出了数字化转型升级“药方”。
2018年,青岛冷箱通过在生产线上部署传感器和物联网设备,采集整个发泡工艺过程中各项参数。这些设备可以与生产设备和系统进行实时连接,并传输动态数据到云平台。工程师们对采集的数据进行处理和分析,以获得生产过程中的关键指标和参数,知道在什么参数组合之下,发泡会出现化学反应不充分。
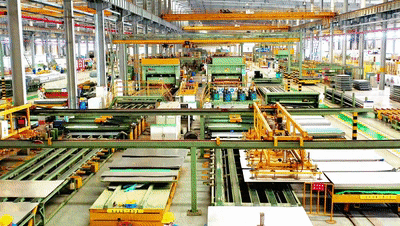
在参数得到精确控制的情况下,青岛冷藏箱质量返修率大幅下降。在不良品率最高的冷藏箱顶板生产中,不良品率下降14%,稳定在2%以内。返修率大幅下降也意味着返修成本的大幅降低,一年下来,可降低冷藏箱返修成本约4万元。
当数据积累到了可观量级之后,青岛冷箱进一步推动工艺智能化升级。通过机器学习算法来推动工艺改善,预测给定生产条件下的不良品概率。例如,通过自动学习和识别复杂的条件变化,可预测生产出来的产品是否为不良品,然后反向优化工艺参数,变“事后分析”为“事前控制”。
集团总部与青岛冷箱协同开发的发泡AI预测APP,包含参数监控、预测注料、质量跟踪、保压监控等功能,工程师们可以通过手机随时随地查看关键参数,出现质量问题可以第一时间做出响应,来达到提升发泡品质。
青岛冷箱通过AI对工艺参数进行精确控制和定制化调整后,发泡液用量持续降低,单张顶板用量从126公斤降至116公斤,实现了发泡板材料成本降低8%。保压时间从开始的35分钟降至目前的28分钟,效率累计提升20%。人工效率从之前的9人天/台,降到现在的4.5人天/台。按照产能最高负荷计算,以前一天只能生产240台冷藏箱,现在可以轻松生产300台,相当于220秒造出1台“大冰箱”。
数字孪生让涂装车间智能化升级
在冷藏箱的生产过程中,还需要大量使用喷漆工艺,漆膜厚度均匀是影响涂装质量的一个重要因素。
青岛冷箱在涂装车间搭建了数字孪生平台,通过物联网平台与产线设备互联,建立产线仿真、工艺仿真。一比一还原真实产线,实现对生产过程的实时监控、故障预测和优化调整,为生产决策提供依据。
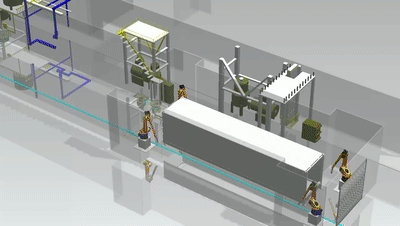
针对漆膜厚度均匀问题,工程师们通过收集机器人轨迹程序,以样板测试喷漆在不同温度、磨损程度、不同压力值下的膜厚、喷漆范围数据,输入工艺仿真软件。将机器人及往复自动喷设备喷漆过程模拟出来,重现现场喷漆过程,在仿真端对比不同参数下的喷漆效果,输出机器人程序供现场参考。
工程师可以直接查看不同的优化解决方案,并在生产之前进行改进。例如,对机器人的喷涂轨迹和速度进行优化和规划、喷涂区域和角度精准地判断等。喷涂参数优化仿真能提高漆膜厚度的均一性,并在满足质量要求的前提下降低油漆消耗。
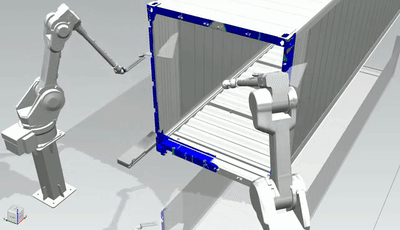
随着智能制造技术和应用的持续推进,国家对智能制造示范工厂的评价体系,已从单点智能、局部自动化,升级到供应链打通和协同,并向价值链上游研发设计和下游销售服务等高价值环节延伸,最终推动生产方式、商业模式和业务形态的创新变革。
在本次揭榜中,青岛冷箱的产品数字化研发与设计、虚拟试验与调试、可制造性设计、智能在线检测、产品质量优化、数字孪生工厂建设、生产计划优化、车间智能排产、产线柔性配置、精益生产管理、智能仓储、安全风险实时监测与应急处置等12个项目典型场景入选。
青岛冷箱以数字化、智能化、绿色化转型为方向,通过智能工厂建设,实现了51%的工序完全自动化,生产数据自动化采集达到75%。智能排产系统将排程时间从2小时大幅缩短至10分钟,人均效率提升50%,单箱能耗降低16%,发泡材料成本节约8%,生产制造周期缩短21.4%,整体交付周期缩短11.6%,以数字化转型赋能企业降本增效的成效显著。

未来可期 中集数字化建设积厚成势
推进两化(即:信息化与工业化)深度融合、加快制造业数字化转型发展,是抢抓新一轮科技革命和产业变革的必然选择,是制造强国、网络强国和数字中国建设的关键路径,也是构建“双循环”新发展格局的重要支撑。
从2018年开始,中集集团开始积极推进两化深度融合和智能制造,聚焦以数字化示范企业作为牵引的核心企业,赋能制造转型和绿色发展,实现降本提质增效。从青岛冷箱和芜湖瑞江开始试点,针对业务痛点,基于工业互联网平台五层架构的数据采集、数据互联、数据管理、数据分析以及业务应用,以生产运行控制、物联网为主实现数据采集和连接,通过数据库和人工智能实现数据治理和数据分析、业务应用。
截至目前,中集集团已经打造12家省级、1家国家级智能制造工厂,实现了工业3.0的跨越。另外,2023年11月宁波中集被工信部评为国家级5G工厂,打造了全国集装箱行业首家5G全连接工厂,为行业树立数字化标杆。
全球制造业正在从以信息化、数字化为主的工业3.0步入以智能化为主的工业4.0阶段。过去几年,中集集团各大业务板块聚焦自动化升级,如集装箱“龙腾计划”、车辆“超级麦哲伦计划”、能化“梦六、梦七计划”等,通过两化深度融合,结合精益的积累,利用数据驱动改善。
下一步,中集将结合“数字中集”五年规划,通过高标引领,力争在集团打造的30家核心企业中实现省级智能制造工厂占比50%、国家级智能制造示范工厂4家,以“全球灯塔工厂”为目标,迈向工业4.0,推进中集智能制造高质量发展。