当医疗领域的高科技遇上工业界的“大块头”,会碰撞出怎样的火花?中集集团旗下南通能源,将用于人体检查的射线技术,巧妙地应用在金属压力容器的焊缝检测上,也是国内首批成功实现该技术的企业。据悉,中集集团正在探索DR与AI技术融合,进一步提升检测效率与精准度,为工业安全构筑坚实防线。
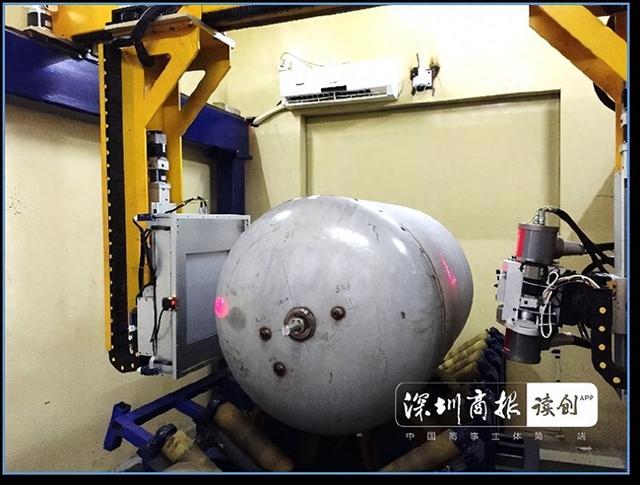
走进南通能源低温制造一车间,在一间不起眼的小房间,身着白色工装的无损检测工程师,一边熟练操控平台,一边紧盯电脑数字成像。身后,两扇紧闭的门扉上,醒目地闪烁着“照射”的警示。
这里是南通能源射线检测室,无损检测工程师正在对压力容器的焊缝,进行无死角、高精度的“体检”,他们也被形象地称为“工厂检验科医生”。
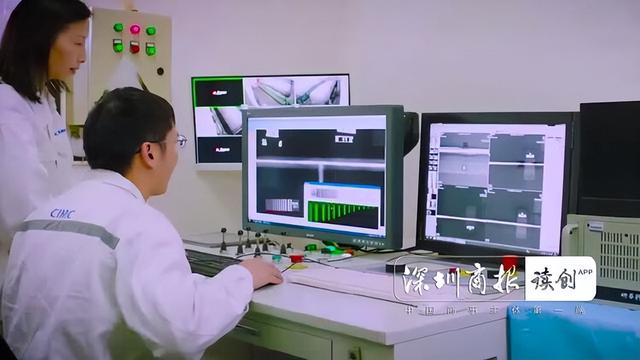
低温压力容器是南通能源的核心产品,能耐受-196℃极低温,通常用于LNG、液氧、液氮、液氢等存储。然而,这些介质极低温的特性,需要高真空多层绝热保温。对容器焊缝质量提出了极高要求,需要100%射线探伤合格,任何缺陷或损伤都可能导致产品失效和安全事故。
但有了DR技术(数字射线检测)的加持,这些隐患都无所遁形。DR技术利用射线穿透物质时的吸收差异,精准识别金属制件中的缺陷。射线检测的过程相当于拍胸片,但检测对象由人变为结构复杂的压力容器,如20英尺低温罐箱,其检测部位近200处。
面对焊缝的多样性挑战,南通能源的无损检测工程师们,采取分阶段实施策略。从简单的封头部件开始试验,并逐步扩展到更复杂的压力容器检测。
2011年经过半年努力,他们完成3000只封头的对比实验,验证了DR技术的可靠性。昔日8人一天检测90只封头,采用DR技术后,仅需4人即可完成140只,一个月节省胶片费用20万元。
按照特种设备安全规范,射线底片需长期存档。对于设计寿命长达20年的产品,底片需同步保存20年,导致企业需建庞大底片档案室管理,成本之高。而DR技术以数字图像存档,无物理空间限制,实现便捷、高效、低成本的长期数据管理。
2017年,为了进一步提升检测效率,南通能源量身定制自动化流水线,并创新研发出智能横梁臂,犹如灵巧的机器人,能够自动响应系统预设,精准锁定每一处待检部位。这一技术革新,大幅提升检测质效。
以20英尺低温罐箱为例,传统胶片检测法,全面检测耗时长达10小时。在引入DR技术及开发自动化系统后,总检测仅需4小时。对于更大尺寸的40英尺低温罐箱,检测效率提升97%。而传统胶片法检测,检测人员要钻入罐体内部,肩扛20—40公斤设备在闷罐中“探伤”。
近年来,南通能源DR检测以创新为驱动,低温罐箱涵盖10英尺至53英尺,低温储罐涵盖1立方至400立方,且开发应用DR爬行机器人,为大型储罐精准“体检”,并已从在制品检测延伸售后诊断,成熟技术与定制化设计铸就行业领先。
截至2024年6月,南通能源已具备5条DR检测流水线,DR检测占比80%以上,共计完成DR拍片量166万张,相当于节省1062万元的射线胶片费用。9名从事DR检测的“工厂检验科医生”全部持证上岗。
南通能源还深度参与《NB/T 47013.11射线数字成像检测》标准制定,推动DR技术标准化,引领行业创新。
面对行业90%仍用低效高价的传统胶片法,南通能源作为行业先锋,不仅引领中集安瑞科旗下中集圣达因、荆门宏图、石家庄安瑞科纷纷跟进,还吸引多家特种设备研究院及重点企业前来“取经”,共推DR技术前沿应用。