一、前言
1.我国炼油工业面临的问题
炼油产能严重过剩
2023年全国炼油能力约9.4亿吨,实际加工量7.35亿吨、同比增长9%,平均开工负荷恢复到79%左右;千万吨级炼油企业达到36家。
成品油消费增速放缓
炼油企业盈利困难
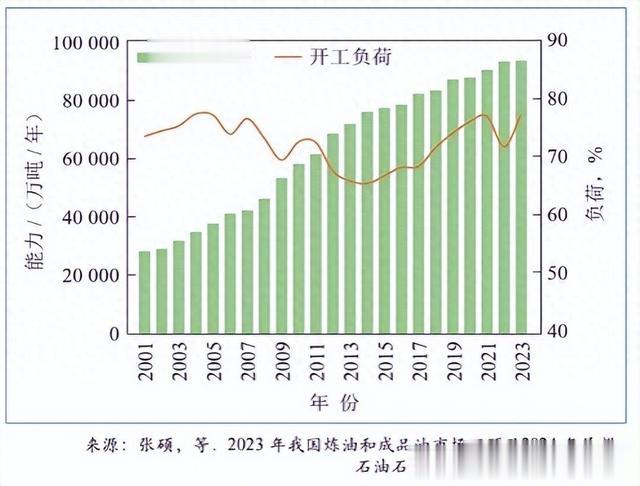
2.我国炼油行业高质量发展要求
关于促进炼油行业绿色创新高质量发展的指导意见 发改能源(2023)1364号
到2025年,国内原油一次加工能力控制在10亿吨以内,千万吨级炼油产能占比55%左右,炼油产能能效原则上达到基准水平、优于标杆水平的超过30%。
推进现有炼厂向组分炼油、分子炼油转变,优化炼油总流程。引导现有炼厂加快产品结构调整和生产技术改造,提高清洁油品、特色油品、化工原料、化工产品的生产灵活性。引导中小型炼厂向科技型方向发展,做精做特,满足区域市场、细分领域需求
依法依规推动不符合国家产业政策的200万吨1年及以下常减压装置有序淘汰退出。对符合条件的以生产沥青等化工品为主、加工特种原油或废矿物油等200万吨/年及以下常减压装置,经国家有关部门认定后允许保留,地方要做好后续全流程监管。
加快劣质渣油低碳深加工技术升级。开发以先进分离技术为基础的组分炼油、分子炼油以及原油(重油)直接制化学品技术,提升原油(重油)催化裂解、低碳烃脱氢、加氢裂化反应过程效率与选择性。
二、化工型炼厂流程分析
1.炼厂类型
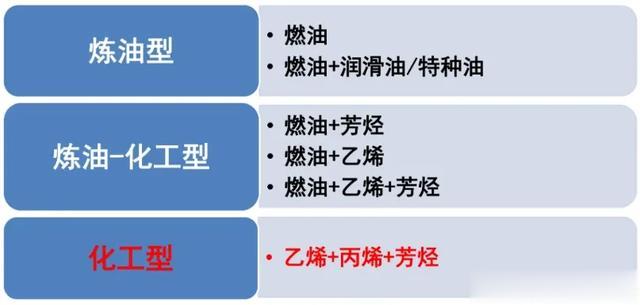
2.加氢裂化型炼化一体化流程
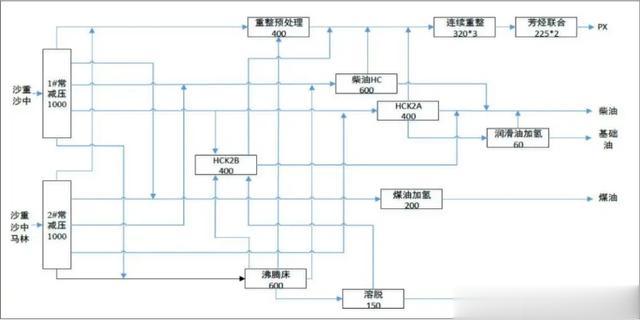
3.加氢裂化型炼化一体化主要产品
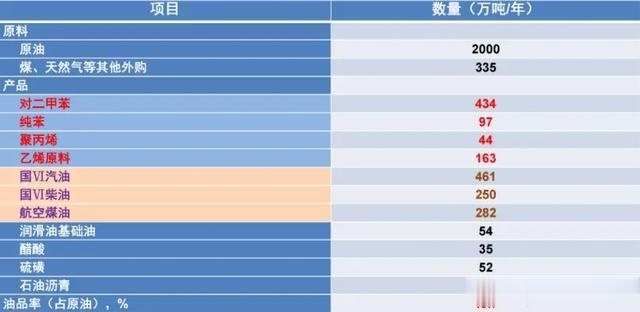
4.催化裂解型炼化一体化流程
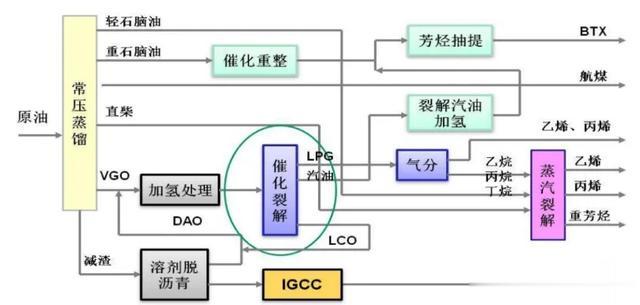
5.催化裂解型炼化一体化主要产品
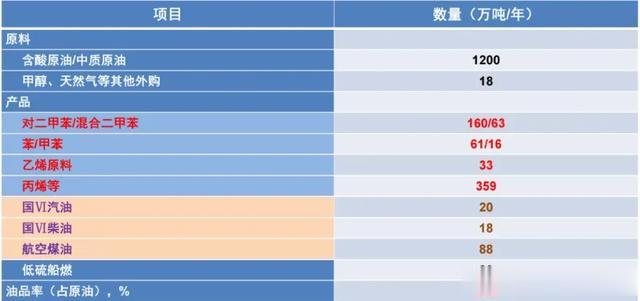
6.RIPP化工型炼厂工业示范
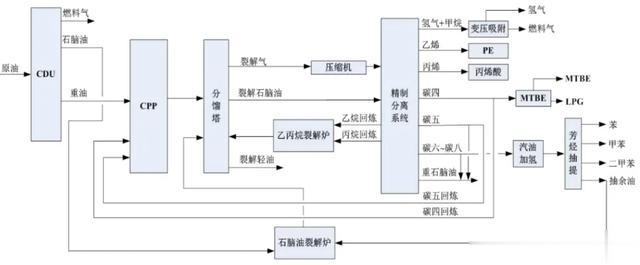
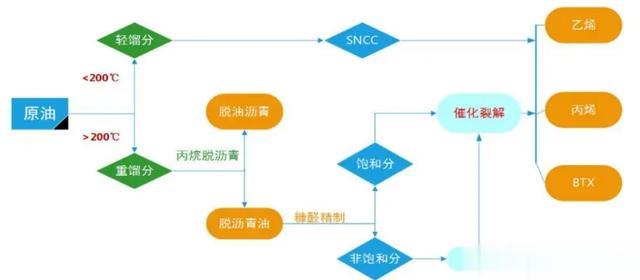
7.中石化原油催化裂解工业示范
石科院自主研发的原油催化裂解技术于2021年4月在扬州石化成功进行工业试验这是原油催化裂解技术的全球首次工业化应用,标志著中石化成为世界上原油催化裂解技术路线领跑者;
采用江苏原油为原料,单程操作,低碳烯烃和轻芳烃总产率达到50%以上
该技术为原油制化学品开辟了一条新的途径,预计化学品收率最高可达70%;
未来这一技术将应用于新建化工型炼厂
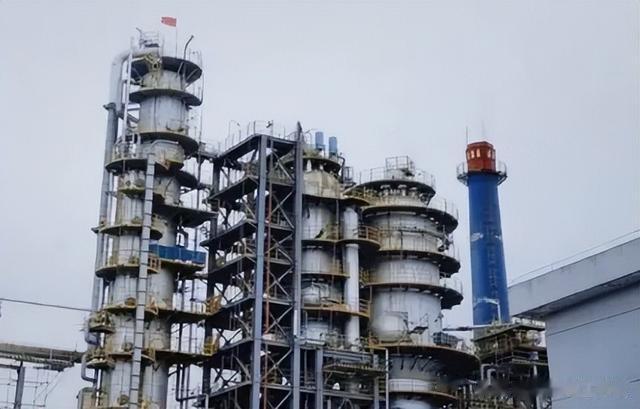
中国石化北京化工研究院、中国石化工程建设公司和天津石化联合开发的轻质原油蒸汽裂解制乙烯技术于2021年11月在天津石化完成了工业试验;
标定结果显示,基于原油的单程化学品收率达48.24%;将大大缩短生产流程、降低生产成本,同时大幅降低能耗和碳排放;
目前,全球仅埃克森美孚、中国石化成功实现了该技术的工业化应用。
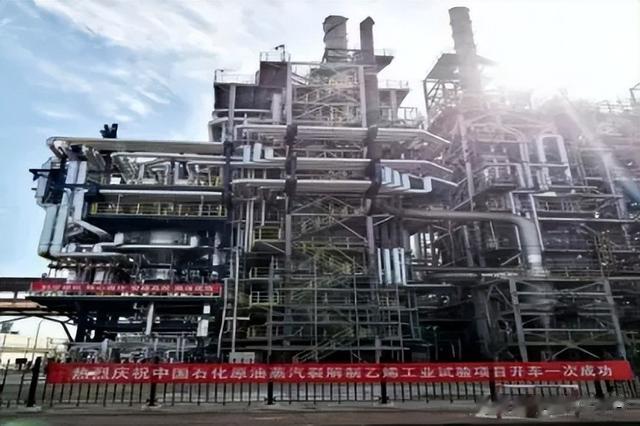
8.不同加工流程适应性分析

9.以催化裂解为核心的化工型炼厂流程
现有炼厂可以通过对催化裂化改造来实现,实现存量资产的增值可以多产化工原料、且种类丰富,有利于后续化工利用;走出一条中国特色的非蒸汽裂解的低成本烯烃生产路线。
三、催化裂解技术及其进展
1.催化裂解技术进展
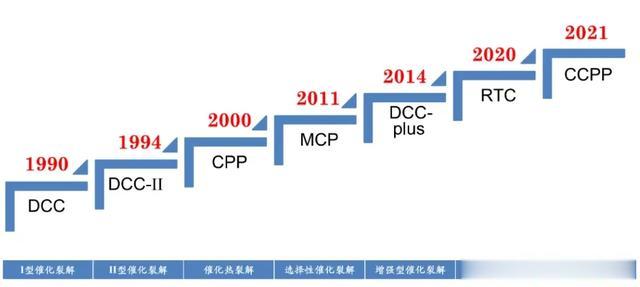
2.DCC技术
中石化自主开发的、国际首创的、以重油为原料生产丙烯和丁烯等低碳烯烃的催化裂化技术。
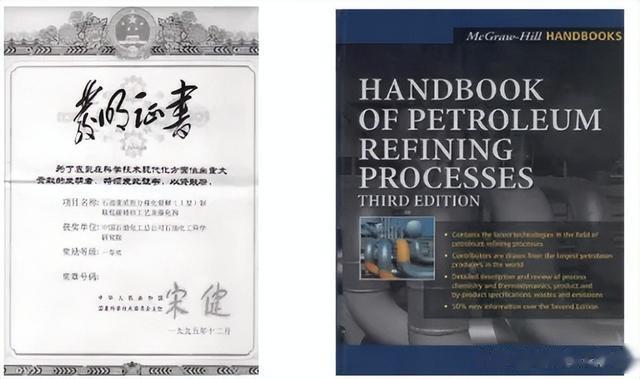
3.DCC技术特点
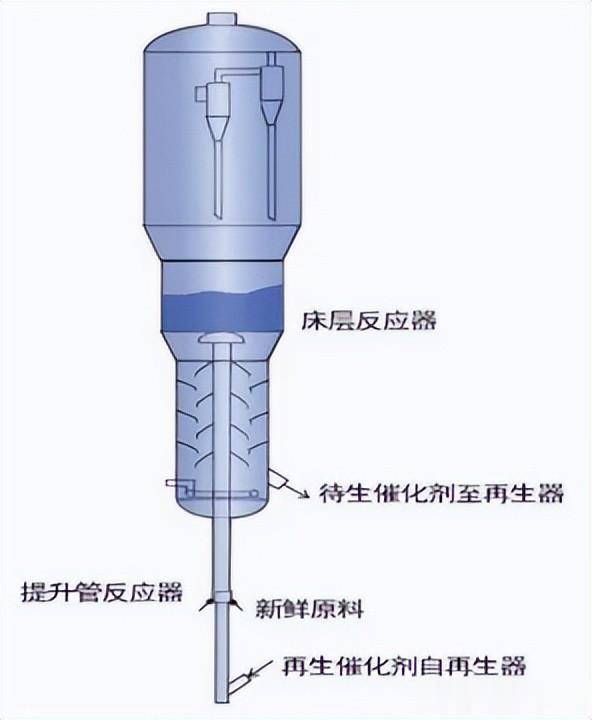
提升管+密相流化床串联组合式反应区结构
新型改性ZSM-5分子筛催化剂
高反应苛刻度
以重质油为原料,丙烯产率高达15~25%
4.DCC-plus反应系统优化
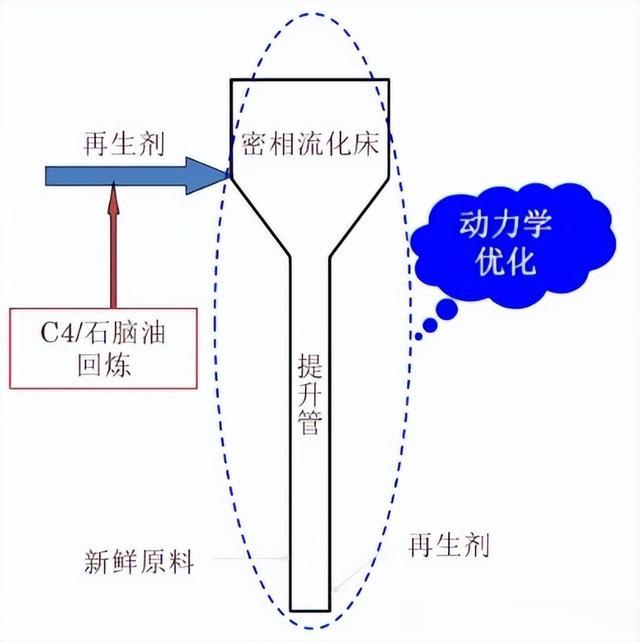
将高温、高活性再生催化剂引入密相流化床反应器从而改变反应器轴向温度和催化剂活性梯度
将C4/裂解石脑油回炼至密相流化床反应器与高温、高活性催化剂接触以满足烃类反应化学需求
对反应器的结构、尺寸和操作参数从反应动力学的角度进行优化以避免过量干气和焦炭的生成
5.DCC-plus中试原料油性质
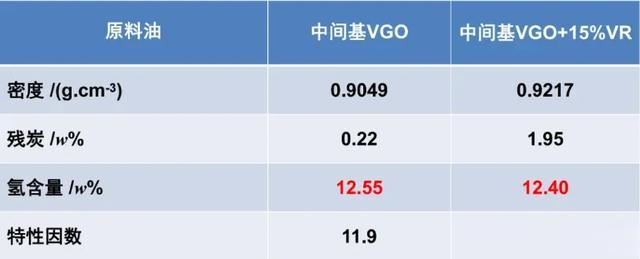
6.DCC-plus与DCC产品产率对比
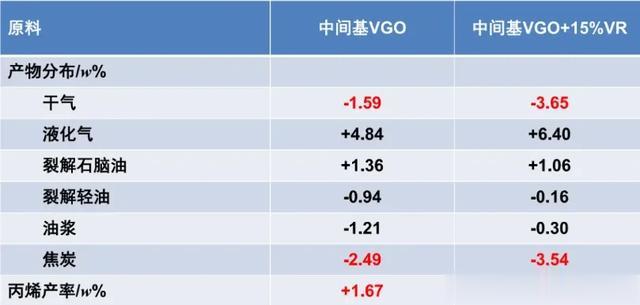
7.大榭石化DCC-plus装置
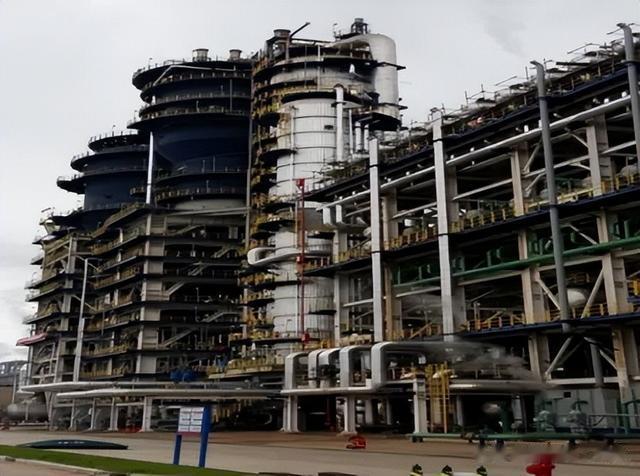
装置规模:220万吨/年DCCplus设计,采用化工型操作模式
设计原料:50%常压渣油+50%加氢尾油混合原料
装置于2016年6月开工,一直平稳运行。
8.大榭石化DCC-plus装置原料性质
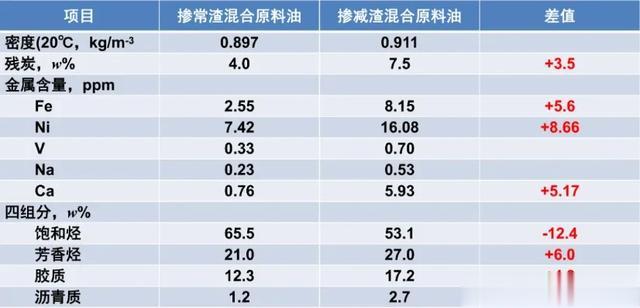
9.大榭石化DCC-plus装置产品产率
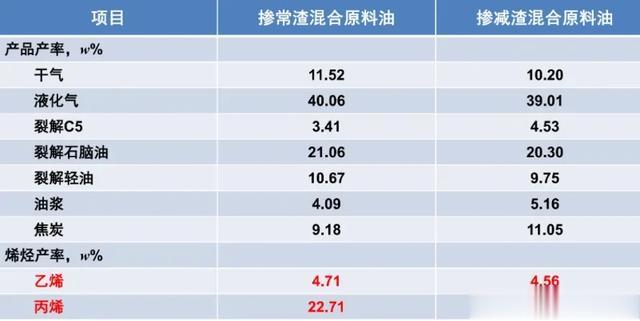
10.DCC-plus装置烯烃和油品方案灵活调整
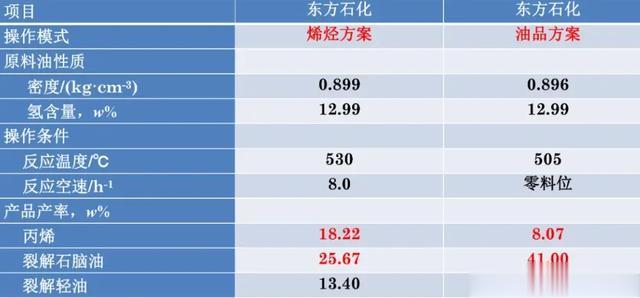
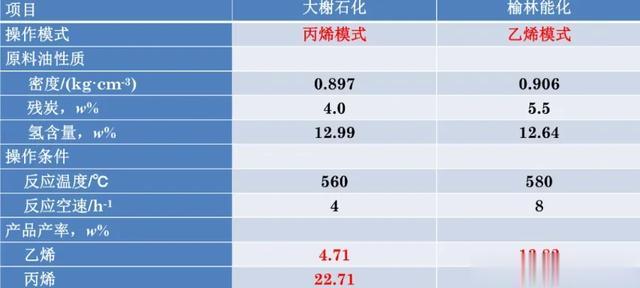
11.RTC技术
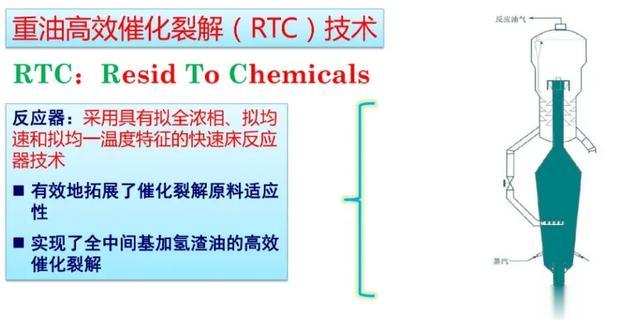
12.RTC技术特点
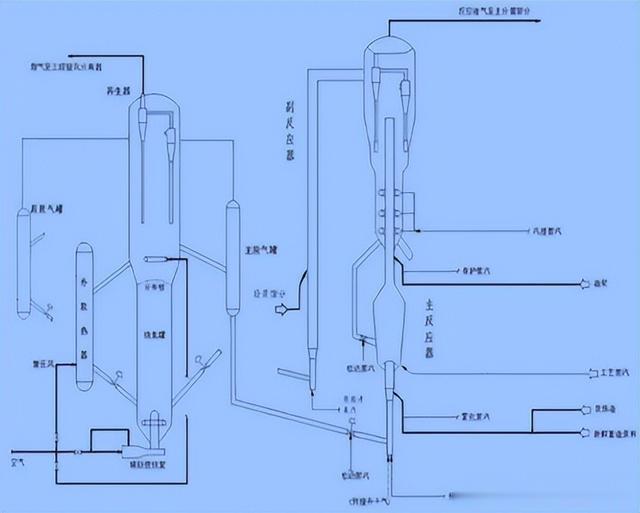
反应系统:
反应器:快速流化床+提升管
反应过程强化技术:
待生催化剂循环技术专用进料转向分配器。专用原料汽油化段、反应器出口区设计等油剂分离:VQS快分+两级旋分
再生系统:烧焦罐+稀相管的高效完全再生
分离系统:分馏、吸收、稳定
双脱系统:干气、液化气脱硫烟气净化系统:脱硝、脱硫、除尘
安庆300万吨/年RTC工业装置
反应系统:
主反应器:新型快速床反应器,加工混合重油原料口 副反应器:提升管,加工C4、C5、RLG柴油、焦化石脑油等
油剂分离:VQS快分+两级旋分
专用的反应过程强化技术
再生系统:
烧焦罐+稀相管完全再生形式
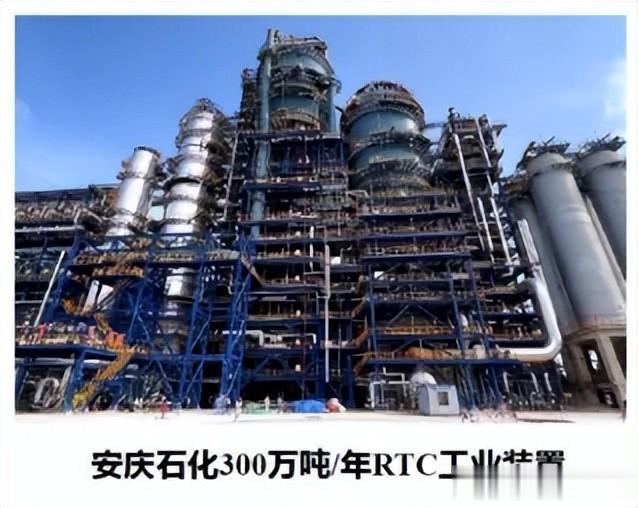
12.安庆300万吨/年RTC装置原料
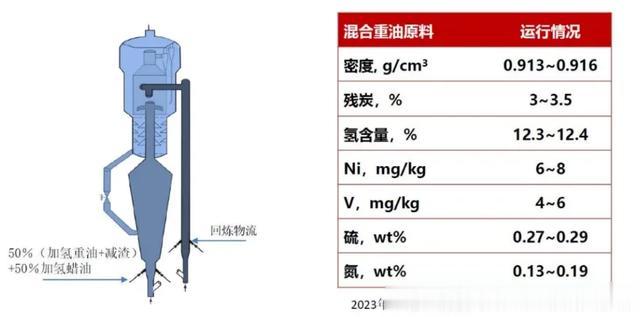
13.安庆300万吨/年RTC装置产品分布
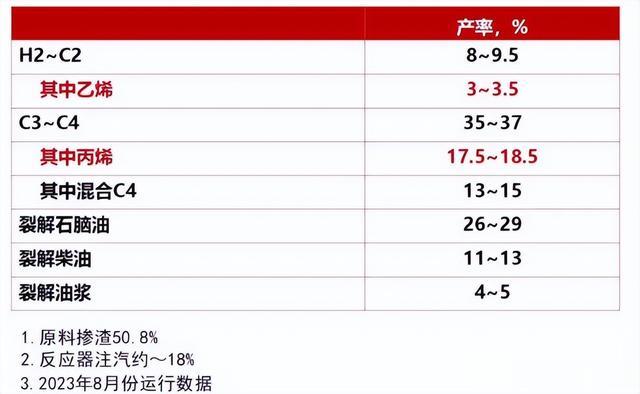
14.CCPP技术
创新性提出 原油直接催化裂解 制化学品技术路线!
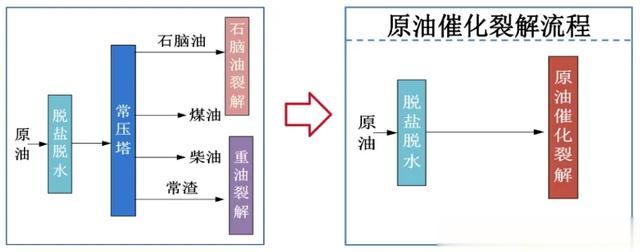
15.CCPP工业示范试验
实现了原油催化裂解技术的全球首次工业化应用
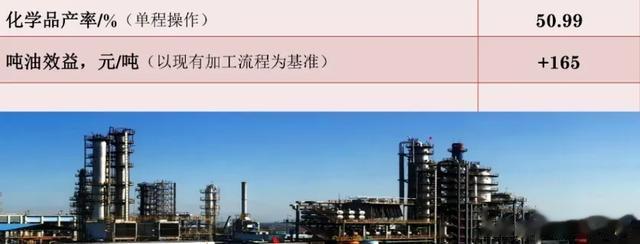
16.CCPP工业试验结果
与现有技术集成,可将中间产物进一步转化成化学品。
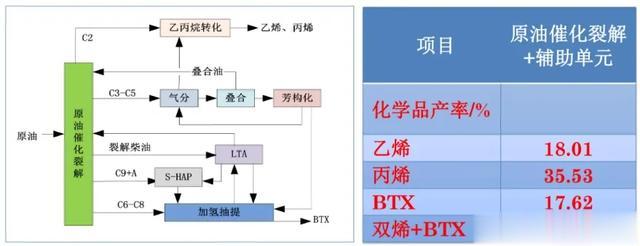
17.催化裂解产品利用技术
干气液相法制乙苯技术
丙烯直接氧化法制环氧丙烷技术
丙烯直接氧化法制环氧氯丙烷技术碳四硫酸/固体酸烷基化技术
丁烯制异壬醇技术
裂解石脑油抽提蒸馏三苯分离技术
裂解轻油制BTX技术
油浆制超高功率石墨电极的针状焦技术轻烃综合利用技术
四,烷烃综合利用系列技术
1.丙丁烷脱氢技术开发
依托石科院先进催化剂PST-100
催化剂性能优异
铂系催化剂,选择性转化率高,废剂易于回收
已得到工业验证
已平稳运行一个全生命周期
依托中石化移动床技术平台
技术经济性优异
反应始终在接近催化剂的最佳活性状态下进行;具有更高的丙烯收率、选择性及更低的能耗
移动床技术成熟
已应用于连续重整装置17套、轻烃芳构化装置1套,工程经验丰富
2.PST系列催化剂性能
2018年,PST-100催化剂在45万吨1年移动床丙烷脱氢装置实现整装工业应用运行结果表明:
催化剂活性高,积炭速率低,在WAIT为630的条件下生产每吨丙烯仅消耗1.16吨丙烷;催化剂强度高,粉坐量低,有利于装置长周期运行;
催化剂持氯能力强,再生注氯量仅为同类催化剂的115,有效提高催化剂的活性稳定性,降低对设备的腐蚀。
2023年,PST-200催化剂在60万吨1年移动床丙烷脱氢装置实现整装工业应用催化剂反应性能优异,生产每吨丙烯仅消耗1.14吨丙烷,待生催化剂碳含量大幅降低,为进一步提高反应苛刻度、提升装置效益创造了有利条件。
3.SPDH丙烷脱氢工艺流程
SPDH包括:预处理、反应、催化剂再生及分离四个部分。
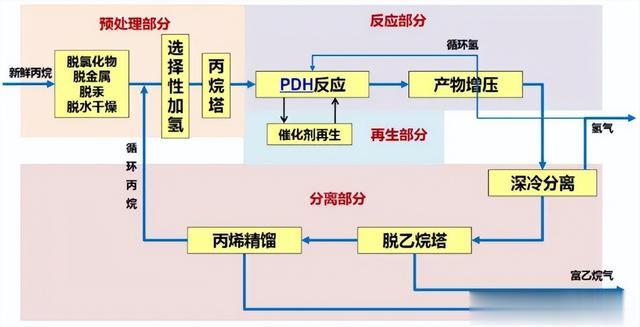
4.丙烷/丁烷混合脱氢工艺流程
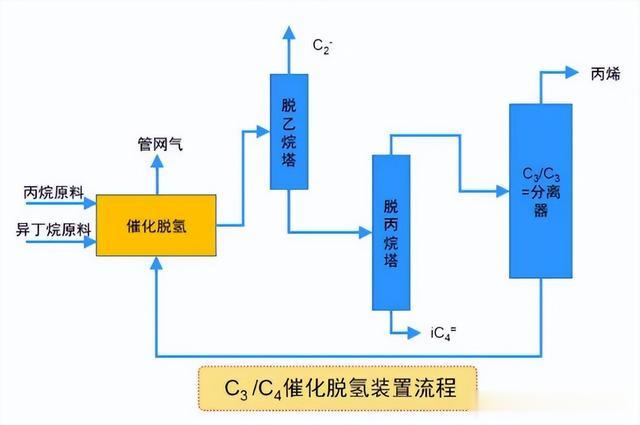
5.轻烃加工技术
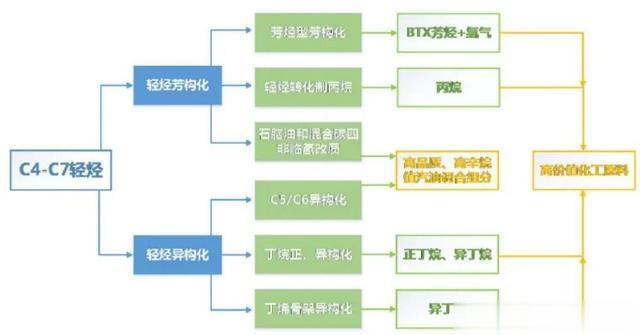
6.轻烃芳构化工艺技术
原料:饱和液化气、混合C4、轻石脑油
工艺:采用择形分子筛催化剂,固体床或移动床,原料无需精制,反应无需临氢
产品:汽油型、芳烃型、丙烷型
7.三种芳构化技术产品对比
汽油型:固定床反应器,主要产品为RON80~93的汽油组分,副产品为饱和液化气(丙烷、丁烷)和少量的干气,
芳烃型:移动床反应器,主要产品为芳烃含量98%以上的混合芳烃其中苯、甲苯、二甲苯占90%以上,副产品为氢气、甲烷、乙烷和丙烧.
丙烷型:[固定床或移动床反应器,主要产品为丙烷,副产混合芳烃和少量干气
8.芳烃型芳构化技术开发
开发了三代催化剂及技术
以轻烯烃和C3以上烷烃,括炼厂气、液化气、混合C4、裂解C5、油田轻烃等为原料
第三代技术采用固定床或移动床反应型式480~550℃℃、0.2~0.5 MPa、0.5~1.5 h-1生产BTX,副产氢气、优质液化气、燃料气
第三代技术已经实现工业化
9.芳烃型芳构化技术工业应用
规模:50万吨/年
原料:14.4万吨/年液化气(异丁烷为主)+13.7万吨/年加氢和重整轻石脑油+21.6万吨/年芳烃抽余油
产品:混合芳烃、氢气、丙烷/丁烷、甲烷乙烷
开工:2020年投产

10.轻烃转化制丙烷技术
原料:丁烷、戊烷/己烷
产品:丙烷、混合芳烃、少量干气
反应条件:非临氢、360~420℃℃0.3~1.0 MPa、0.5~1.0 h-1
工艺特点:固定床或移动床
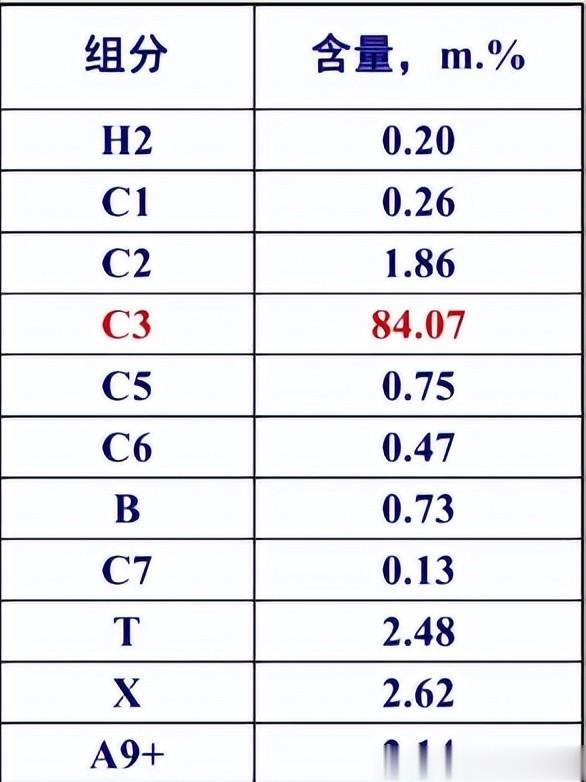
原料:C5/C6轻石脑油
产品:丙烷、混合芳烃、乙烷/甲烷
反应条件:非临氢、360~420℃℃0.3~1.0 MPa、0.5~1.0 h-1
工艺特点:固定床或移动床
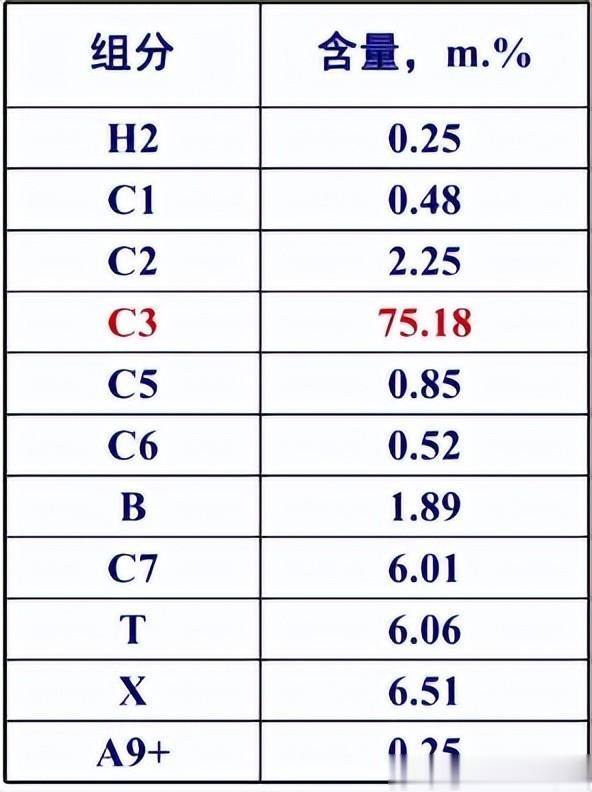
在我国炼油能力日益过剩、成品油需求增长放缓、替代能源迅猛发展等多重压力下,多产化工原料和化学品、以及绿色低碳是未来炼厂转型的发展方向:
以DCC技术为代表的多产低碳烯烃催化裂解技术仍然保持世界领先的技术水平,业已工业验证的DCC-plus、RTC和CCPP等技术具有较强竞争力;
重油催化裂解、烷烃综合加工等技术集成,是构建新一代化工型炼厂的具有竞争力的技术选择,是发展中国特色的非蒸汽裂解的低成本烯烃生产路线。

来源:经燕化工平台网络综合整理