来源:机器故障诊断与全寿命周期管理
如果在离心泵的叶轮人口处由于液流局部速度过大而出现负大气压区,而且该负压区的压力低于被抽送液体的饱和蒸汽压时,液体就会产生蒸汽化。流体将汽泡带人高压区并在该区中破裂。汽泡破裂时会产生极高的局部压力峰值,从而有可能导致设备的损坏。在这种情况下,如果使用合适的检测仪器,就可以通过测量离心泵出口壁上的固体结构噪声或泵入口处的流体噪声来显露这种内破裂。这种检测方法是目前测量汽蚀过程最为简便的一种方法,通过这种检测完全能够证实汽泡破裂产生破坏危险的真实性。
通过对汽蚀噪声的测量能够确定所有型式的汽蚀现象。这一方法甚至可以进一步应用于与金属表面不接触的汽泡中和受压侧的汽蚀区中。所有能够影响流体汽蚀强度的因素同样都会对汽蚀噪声产生影响。在通过声压检测结果对汽蚀现象进行诊断的过程中,测量信号的强弱也就表明了汽蚀的强度,因为声压的大小是随着破裂汽泡数目的增加而增高的。基于这种联系,表明汽蚀的形成以及汽蚀噪声与腐蚀的内在联系就显得十分必要了。不管怎样,由于汽蚀噪声的大小仅仅只是汽蚀强度的间接测量值,而实际上其值在很大程度上取决于测量仪器的放置状态,尤其是所选择的频率范围。
一、离心泵中的汽蚀噪声
在保持恒定流量和恒定转速的条件下进行泵的吸人性能试验时,可以在泵的吸入口放置一个压力传感器以测出逐渐降低的吸入压力值并以信号显示。图1中示出了这些信号。
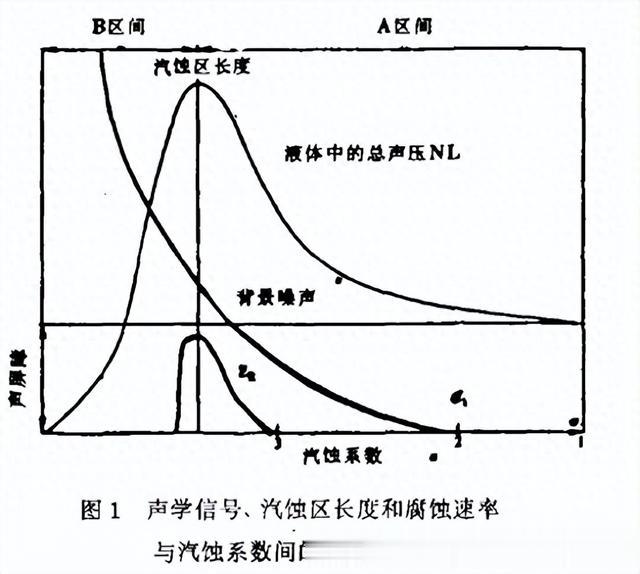
1,声学仪器接收汽蚀噪声信号;
2,可见液中发生汽蚀;
3,开始对流道固体边壁产生腐蚀。
可以在泵的吸入压力超过汽蚀形成压力的时候,测出泵的背景噪声值。泵的背景噪声是由液体的紊流、叶片的不稳定作用力以及机组设备的机械噪声引起的,而与泵的吸人压力无关。汽蚀生成之后,汽蚀噪声的大小会随着泵汽蚀系数的减小而增高。噪声先达到某个最大值(A区间),然后陡然下降,常常会低于背景噪声值(B区间)。值得一提的是,由于汽蚀所导致的材料损失率也具有一个相似的图形(图1)。曲线上出现最大值的原因是:随着汽蚀系数的减小,蒸汽的体积(汽泡的尺寸)和汽泡的数量均会增大,并同时伴之以驱动压差值成线性减小。在这一过程中产生的另一个现象是:在一些小的空区中,某些破裂的汽泡于体积的变化所产生的汽蚀噪声的上升值为:
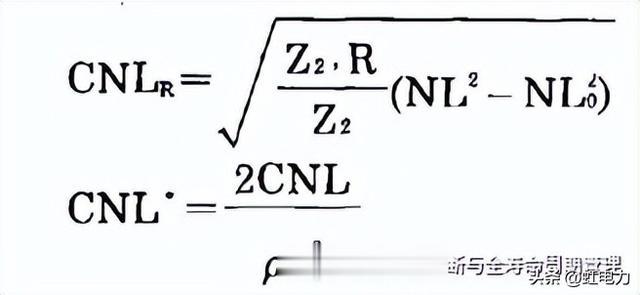
这样一个标准公式是如此切合实际,而且还通过实验得以证明。
二、汽蚀噪声的频率特性
汽蚀通过非周期性的脉动而产生噪声,这种非规律性脉动所产生的噪声通常与脉动时间、峰值以及脉动后果有关。脉动所产生的噪声有一个很宽的频谱,频谱上的能量分布有一个很宽的高峰值。这一高峰值处于汽泡破裂次数最为频繁的区间。
通过频闪观测法对叶轮中形成汽蚀现象的观测可以证明(图2),当汽蚀区的长度增加时,汽泡区出现波动(频率低于1OkHz )。这种现象的出现将会对汽蚀噪声产生明显的影响,并且可采用Strouhal数来表述(s=0.3+10%)。这一高频部分是由单个汽泡的破裂所造成的(频率范围10kHz~1MHz)。
汽泡区域的波动是由紊流和非轴对称的入流参与叶轮不稳定性流动引起的。这种流态通常出现在多级泵的入口处、叶轮的导向翼板或导向叶片四周。也许是由于汽蚀区域的变化在一定程度上能使汽泡的破裂现象得到调节,并影响到汽泡从生成位置至破裂位置的转移。
目视结果表明,随着汽蚀系数的减小,汽泡区域的波动将会明显地加剧。因此我们能够预计到,汽蚀噪声频谱的低频部分将会随着汽蚀系数的降低而增大。试验证明,气体的含量有明显的影响(特别在频率小于10kHz的时候)。在反弹状态下,汽泡的破裂将造成一个高压峰值和一个低压谷值。
根据参考文献中所列出的论据,在下述频率下会在汽蚀噪声频谱上出现最高振幅:
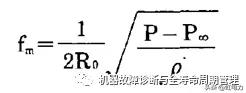
式中的汽泡半径R。和局部压力P为未知值,但其间的比例可用下述关系式大致获取:
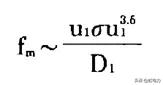
这表明,最大能量密度的频率值直接取决于汽蚀系数。这种关系与我们观察到的并且在文献中所表述的结果相一致。可以将这些结果大致概括为如下三点:
1、随着NPSH的增加、转速的提高或汽蚀系数的增大,汽蚀噪声频谱上的最大能量密度将向高频区转移。
2、如果试图通过汽蚀噪声的测量来确认汽蚀强度,就必须在尽可能宽的频率范围内进行噪声测量。特别要注意低频部分的噪声测量,因为常常会把汽泡区的自振想当然地归结于汽蚀破坏。如果汽蚀噪声的测量值超过了一个狭窄的频段,那么在运转工况改变的时候所测得的频段就有可能取代含最大能量密度的频段,这样就能在对结果进行解释时修正所提出的结论。噪声的测量通常只是在相对狭窄的频段内进行,而频段的宽度是任意选定的。因此,测试的结果很难与其它方式测得的结果相比较。
3、如果测量汽蚀噪声的目的仅仅是为了表明汽蚀是否形成,那么这种测量就可以选在一个高于背景噪声值的频率范围内进行。
三、对流体噪声产生腐蚀危险性的估计
根据以前的调查结果,可以确定出在频率为1~180kHz的范围内腐蚀比能与噪声强度之间的关系。
利用等式:
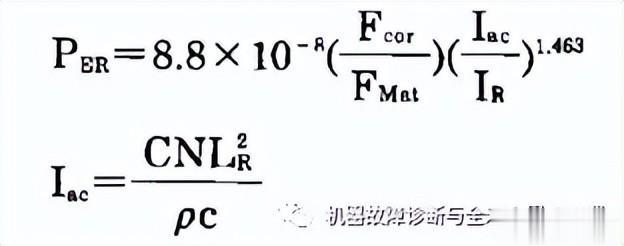
腐蚀率可以从流体噪声的测量值估算而得,不管怎样,问题的关键在于在水泵装置中进行测量时其进口压力通常是不能改变的,因此也就不可能决定其背景噪声值。为近似起见,可以利用总噪声值。目前对汽蚀进行研究的现状大抵也是这样:
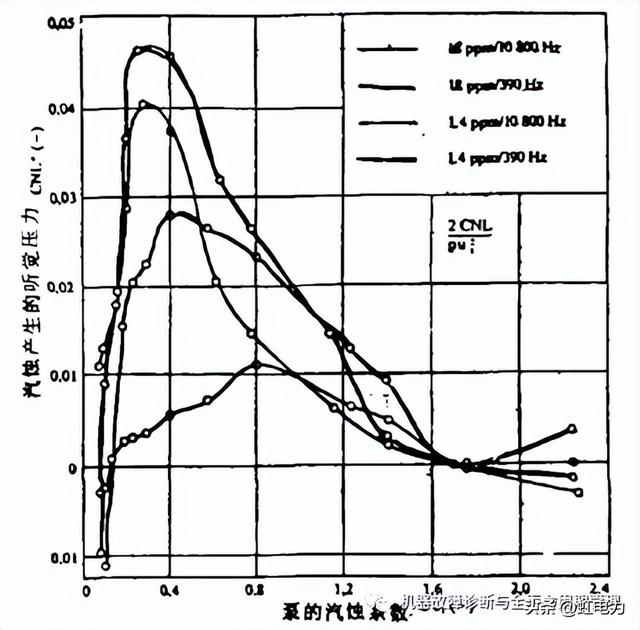
图2 空气中含量和频率变动范围对汽蚀噪声的影响
被测信号的量值越是接近于背景噪声值的大小,测量的可信度就越差。如果所装叶轮的性能为已知,那么可视汽蚀的生成就可以大致上被估算出来。利用装置的汽蚀系数,就能够估算出汽蚀的发生是否符合预料的结果。
在叶轮的入口角较大和旋转叶片入口边形状不当的情况下,系数为2是不足为奇的。在装置的汽蚀系数值大约为0.5时,通常将产生汽蚀现象。如果汽蚀系数介于0.2~0.3之间,就可能形成B区间(见图1)这时所测得的声压就是在无汽蚀破坏情况下的值。
在装置上进行噪声测量时,只能利用频率大于lOkHz的高频声波。然而在低频声波被滤出的情况下,所得到的曲线特性和声级值就可能与真实值之间存在着明显的差异(图2),这时候所测得的声压值不再是一种代表流体汽蚀强度的量值。如果在装置上利用不同的频率进行测量,就可以确认出低频噪声仅仅是总噪声值的很小一部分。在可能利用范围为10--18OkHz间的声压的情况下,就可以认为频谱上的这一部分噪声实质上是由汽蚀所产生的。
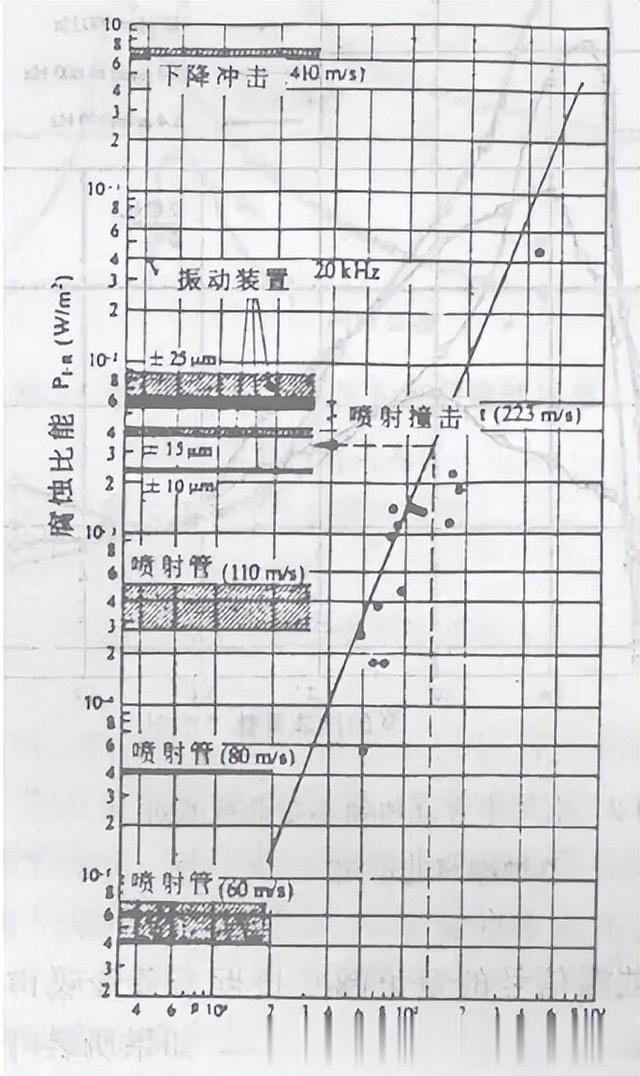
图3 腐蚀比能与破裂压力间的函数关系
四、对腐蚀开始的评估
流体噪声是对流体汽蚀强度的一种度量。遗憾的是,所测得的声压值远比汽泡破裂压力小。因此,如果腐蚀的开始被确定,那么材料的绝对强度(用破裂压力表示)与所用材料的抗汽蚀性能有关。
如果在某个确定的空间点测量噪声,那么声源的声能可以根据相关空间的声学特性计算而得。通过对声学系数(发射的声能与破裂过程中机械能的比值)的估算,可以近似计算出破裂压力。然后将材料所受的应力与其疲劳强度相对比。
图3表明了所测得的材料腐蚀量与按测得的噪声计算出来的破裂压力之间的关系。因为材料的绝对应力是由破裂压力引起的,所以可以将不同的试验结果引人图表中。在冲击腐蚀减小的情况下,冲击压力可按Pi =cρω计算而得。
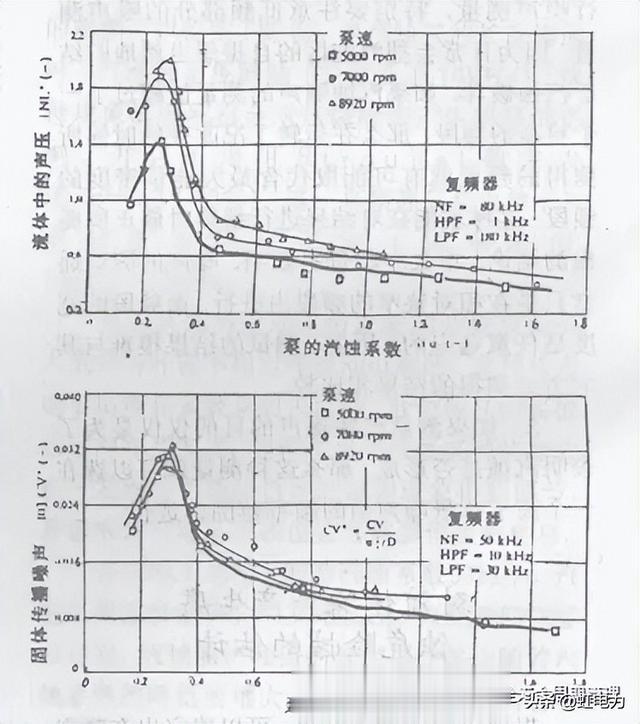
图4 流体传播噪声和固体传播噪声与汽蚀系数间的关系曲线
五、固体传播噪声的测量
在进行流体传播的噪声测量时,必须在吸人接管处钻一个孔以便放置压力传感器。另一方面,可以在泵体的外壁面上进行固体传播噪声的测量而不必穿透被测系统,这也是一种被推荐为测量固体传播噪声的行之有效的方法。和流体传播噪声的测量方法一样,固体传播噪声的测量也应在一个较宽的频谱段范围内进行。
图4表明,在10kHz~30kHz频率范围内的固体传播噪声和所测得的流体传播噪声一样都是汽蚀系数的函数。流体传播噪声和固体传播噪声的曲线相对于汽蚀都具有相似的特性。
如果把腐蚀比能当作固体传播噪声的函数,就可以发现腐蚀与所测加速度之间没有通用的关系。这并不是我们所预料的,因为流体传播的噪声进人壳壁的传递和固体传播的噪声在壳壁内的传递均取决于其几何尺寸和材料。然而,对于一个给定的系统,腐蚀与固体传播噪声之间总是存在一定的相互关系。为了获取在腐蚀与壳壁加速度之间能够实用的关系,我们可以谋求通过一个简单的声学模型所测定的加速度来计算出流体传播的噪声。能量统计分析法给这种计算提供了可能性。这种可能性是基于液体中的声场属宽频带型而且具弥散性和高频性这样一种假设。还可以进一步假定在已知的频率范围内存在大量独立的模型,既包括载液空间又包括四周边壁。
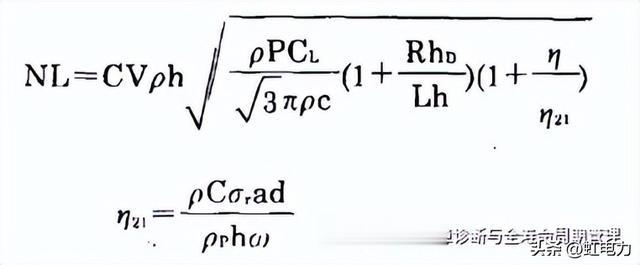
在应用这种方法时,要将腐蚀比能作为固体传播噪声的函数通过计算转换成腐蚀比能作为流体传播噪声的函数,很明显,这些由固体传播噪声的测量所得数据组作为流体传播噪声函数的腐蚀修正值。尤其值得说明的是,这种试验是在空气中进行的(对于这些试验,不能考虑恰如其分地将CNL标准化成相关的叶片数)。
由于试验所用的声学模型是近似的,同时声音的吸收与声音的传递一样都与很多参数有关,其中包括管道的连接和基础,另外也要考虑与这种计算方法相关的不定性因素和分散量。此外、由于至今尚未确立出一套完整的测量技术,因此这些测量数据是从不同的频带处获取的。
如果能够测出固体传播噪声与流体传播噪声之间的转换函数,或者至少测出其频谱并对每一频带进行计算,就可以明显地改善这一过程的精度。
应用从固体传播噪声计算流体传播噪声的声学模型具有能够估算破裂压力的优点并由此能获得材料的绝对负荷值。
对固体传播噪声频谱的测试表明,同样的低频部分,其量却很小。因此没有必要对固体传播的噪声确立背景噪声值。不管怎样,由于噪声源数(叶片数)对固体传播噪声具有明显影响,因而固体传播的噪声会随叶片数而变化。
六、相对腐蚀强度
对第一次近似值,由于取流体中的声压与所测得的加速度成正比,因此在下面的关系式中可以对加速度和声压取相同的指数值。

根据试验结果,可以取x=y=2.92。为了优化起见,可以得到相对的腐蚀强度。相对腐蚀强度是在特定环流速率下的腐蚀率,该腐蚀率是指最佳点(或其它任何基准点)的腐蚀率。
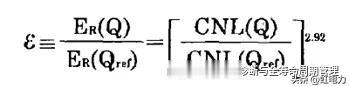
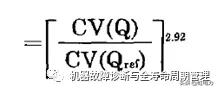
利用这一关系式就可以在不同的运转条件下(如温度、气体含量、吸人压力等)针对不同的负荷估算出腐蚀危险率。
当利用其它频率范围进行测量时,可以以此为例借用这一方法。
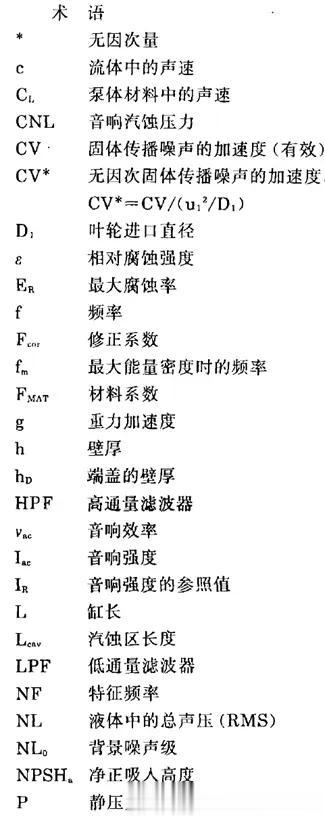
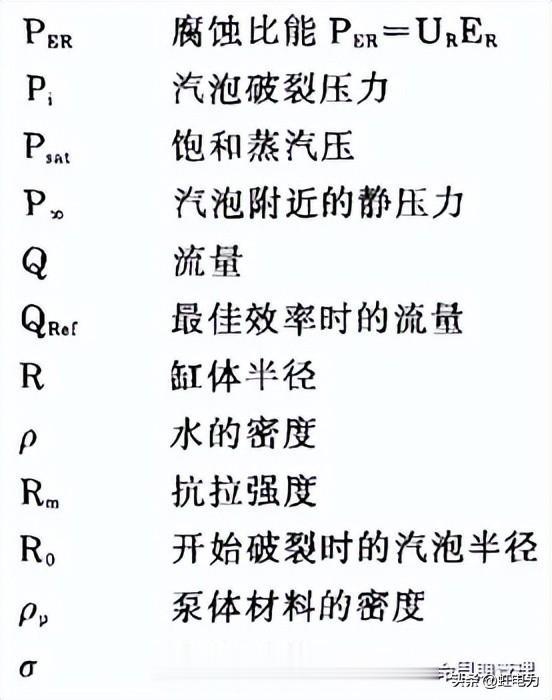
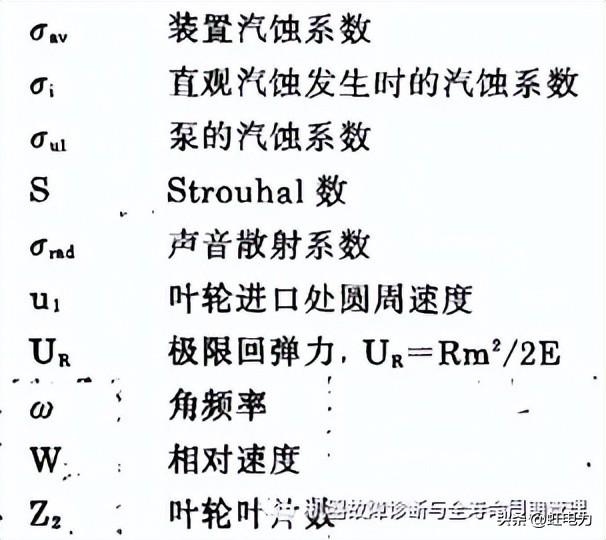