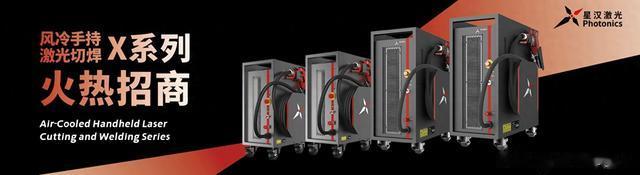
点焊是一种高速、经济的连接方法。它适用于连接不要求气密的搭接接头薄板构件。点焊的种类很多,如电阻点焊、电弧点焊、胶接点焊、复合点焊,还有激光点焊等。当前生产中应用较为广泛的应属电阻点焊,以汽车工业为例,在车体面板的部件装配过程有 3000~4000个焊点,共需要250~300台机器人来完成这一任务,还要包括配套的控制系统和其他辅助设备等。由于电阻点焊的灵活性较差,在经济高速发展的今天,汽车部件的几何形状与结构更新周期非常短,新产品新型号的更新换代需要一种高效、灵活的新型点焊技术来适应。
因此激光点焊技术逐渐成为人们关注的焦点,有望大量应用于汽车工业生产中。在航空航天领域,激光点焊也作为一种替代技术在进行试用,长期以来,航空、航天产品的搭接接头一般都采用铆接的方式,生产工序多、工作量大。
随着铝合金、钛合金、复合材料等新型材料的应用越来越广泛,采用新型的焊接技术取代传统的连接方法已经成为一种主流趋势。它不但能够增加生产效率,而且还能减少结构质量和满足新的结构设计,这对于航空、航天产品具有重要意义。激光点焊所具有的高精度、高柔性的特点使其在实际生产,特别是航空工业的应用中能够取代传统的电阻点焊和铆接等工艺具有很大优势。

一、激光点焊的特点与定义
定义:
激光点焊是指在同一位置上由单一的激光脉冲(t>1ms)或一系列激光脉冲来熔化和连接焊件。
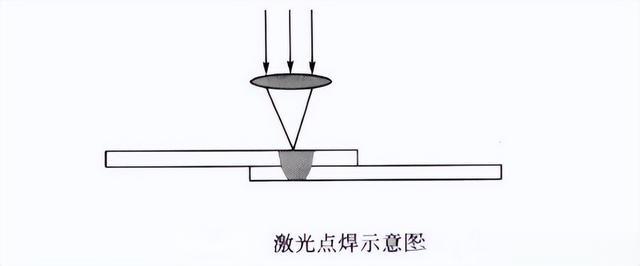
激光点焊与其他的激光焊接过程基本相似,唯一的区别就是点焊时激光束与工件之间没有相对位移。激光点焊分为热导型和匙孔型两种方式。热导型点焊时激光仅能使金属熔化,但不能使金属气化,这种点焊方式比较适合焊接厚度小于0.5mm 的金属,如采用 Nd:YAG 激光点焊电子元件等。在匙孔型激光点焊中激光可以通过匙孔直接入射到材料内部,激光能量的利用率增加,可产生较大的熔深传统的电阻点焊是通过电流产生的电阻热来熔化工件形成焊点,激光点焊的热源来自于激光辐射,所以形成的焊点形状有很大区别。
激光点焊的可调参数一般为激光功率、点焊时间和离焦量,采用脉冲方式点焊时还包括脉冲波形,频率和占空比等。其中激光功率主要影响焊点的熔深,而点焊时间则对焊点横向尺寸有较大影响,一般激光作用时间越长,焊点的上下表面尺寸和熔合面尺寸越大。离焦量变化主要是作用于工件表面的光斑大小和能量密度,因此对焊点整体形状都有较大影响。
特点:
(1)、由于采用激光作热源,点焊速度快,精度高,热输入量小,工件变形小。
(2)、点焊位置的自由度大大提高,可以实现全位置点焊,而且很容易实现单面点焊,因此产品设计的自由度也有很大提高。
(3)、激光点焊对搭接接头尺寸的要求不高,接头搭接量,焊点之间的距离等参数的限制很小,不需要考虑电流分流的影响。
(4)、对于不等厚板、异种材料和特殊材料(铝合金、镀锌板)的激光点焊性能要比传统的点焊方式有优势。
(5)、不需要大量的辅助设备,能够较快的适应产品变化,满足市场需求。
二、激光点焊缺陷分析
裂纹、气孔和下塌是激光点焊最常见的缺陷,下面进行逐一分析。
1.裂纹
裂纹分为表面裂纹和纵向裂纹。激光点焊过程的加热和冷却速度非常快,加热区与周围金属之间的温度梯度大,比较容易形成裂纹。裂纹的产生与材料有很大关系,如铝合金的激光点焊裂纹倾向就比不锈钢大得多。采用优化脉冲波形控制金属凝固过程的冷却速度、降低内部应力是抑制裂纹产生的一种有效方法。
2.气孔
激光点焊焊点中的孔状缺陷气孔可分为小气孔和大气孔两种情况。小气孔主要由于金属凝固时氢在液态金属中的溶解度下降,及匙孔中金属的急剧蒸发和熔池挠动产生的。大气孔主要是由于激光点焊的过程冷却速度太快,匙孔外围的金属没有充分时间回填造成的。一般来说在长脉冲的点焊方式下容易产生小气孔,而短脉冲则容易造成大气孔的产生。
在激光点焊中气孔最易出现的两个部位,一种是在焊点中部熔合区附近,另一种则是焊缝根部。X射线方法拍摄到的熔化图像表明,熔合区附近的气孔主要是因为匙孔闭合时产生缩颈所导致的;对于焊缝根部气孔,主要是由于形成匙孔之后激光的迅速消失,匙孔崩塌而形成。
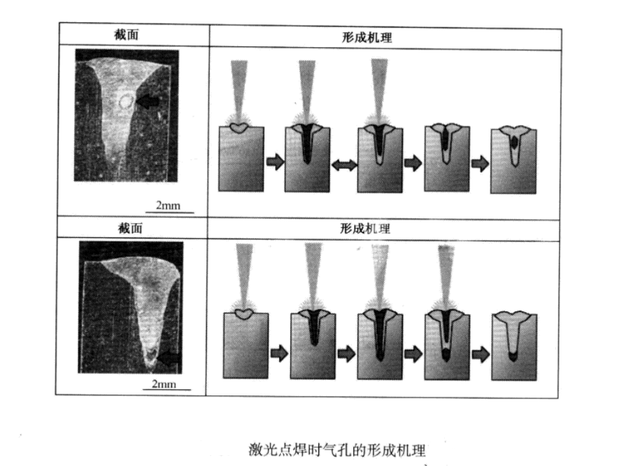
3.下塌
下塌是激光点焊中一个很明显的现象。焊点表面出现的中心下塌和四周金属堆积现象是由于金属气化产生的反冲力把液态金属推向焊点表面,而在冷却过程中表面堆积金属快速凝固来不及完全回填而形成的。此外,金属急剧蒸发和飞溅造成的材料损失也是形成中心下塌的一方面原因。脉冲时间对焊点表面的下塌、气孔的形成都有较大的影响,通过优化脉冲波形与时间可以得到满意的焊点。
4、离焦量对焊点焊的影响
离焦量的变化直接改变了光斑直径与能量密度的大小,离焦量向负方向和正方向增大时,都意味着光斑直径的增大和能量密度的减小。在激光点焊过程中,光斑直径与激光入射在试件上所形成的初始匙孔大小存在一定的对应关系,而能量密度则决定了熔池的扩展速度。当离焦量绝对值较小时,激光光斑直径小,激光功率密度大,焊点熔池扩展的速度较快,但初始匙孔的直径小;相反情况下,离焦量较大,初始匙孔的直径大,但是熔池扩展速度变慢,得到的焊点尺寸不一定很大,故在离焦量的变化过程当中光斑直径和焊点表面功率密度的综合作用决定了焊点尺寸的大小。
三、激光点焊技术的应用
由于激光点焊速度快,深度大,变形小,能在室温或特殊的条件下焊接,焊接设备简单。此外,随着高频率的脉冲激光器的出现(高于每秒40个脉冲),使得激光点焊大量应用于批量自动化生产的微、小型元件的组焊中。在焊接一些小的电子元件中,要求较小的热影响区,如玻璃与金属的连接,热敏感半导体电路中接头的连接,以及电线中不同金属之间的连接等,这些领域中激光点焊比传统的点焊工艺(如电阻点焊)更有优势,且焊点无污染,焊接质量高。图6-60所示为激光点焊在汽车车灯生产上的应用实例,一个500W的固体脉冲激光器,用很高的脉冲频率来产生四个相似的焊点。
在利用高脉冲能量对微小结构进行高精度点焊时,脉冲Nd:YAG激光器具有技术上和经济上的优势。在绝大部分的工业点焊应用中,基本上都使用平均功率为50W且脉冲功率>2kW的脉冲固体激光器,激光可通过光纤或组合式聚焦透镜直接作用在工件上。
激光点焊适用的材料范围很广,例如,在点焊Li电池时,使用Nd:YAG激光点焊技术来连接不同的金属比采用TIG和电阻点焊都更有效率,特别是由于生产时采用光纤来传输激光,可以很方便地在各个工作台间快速、灵活地移动。
综上所示激光点焊具有以下特性:
(1) 随着激光功率的增加,焊点表面直径出现上下波动,熔合面直径和下表面直径增长缓慢。焊点截面形态的变化不明显。而随着持续时间的增加,焊点尺寸增长很快,熔合面直径的变化速率要大于上下表面直径的变化速率。离焦量的变化对焊点尺寸的影响很大。它直接改变了光斑直径和激光功率密度,这两者的综合作用决定焊点尺寸的大小。
(2) 在熔透情况下,激光点焊的焊点表面存在明显的下塌。随着激光功率和持续时间的增加,焊点表面的下塌深度增大,在持续时间或者间隙尺寸较大的情况下,下表面还会出现内凹。
(3) 随着间隙的增加,焊点整体变形,中心的下塌和内凹都很明显,且熔合面出现收缩现象,强度下降很快。目前在焊接电阻、电池及电子领域常用同时焊接两个点的工艺,通常采用两个激光光源设计。